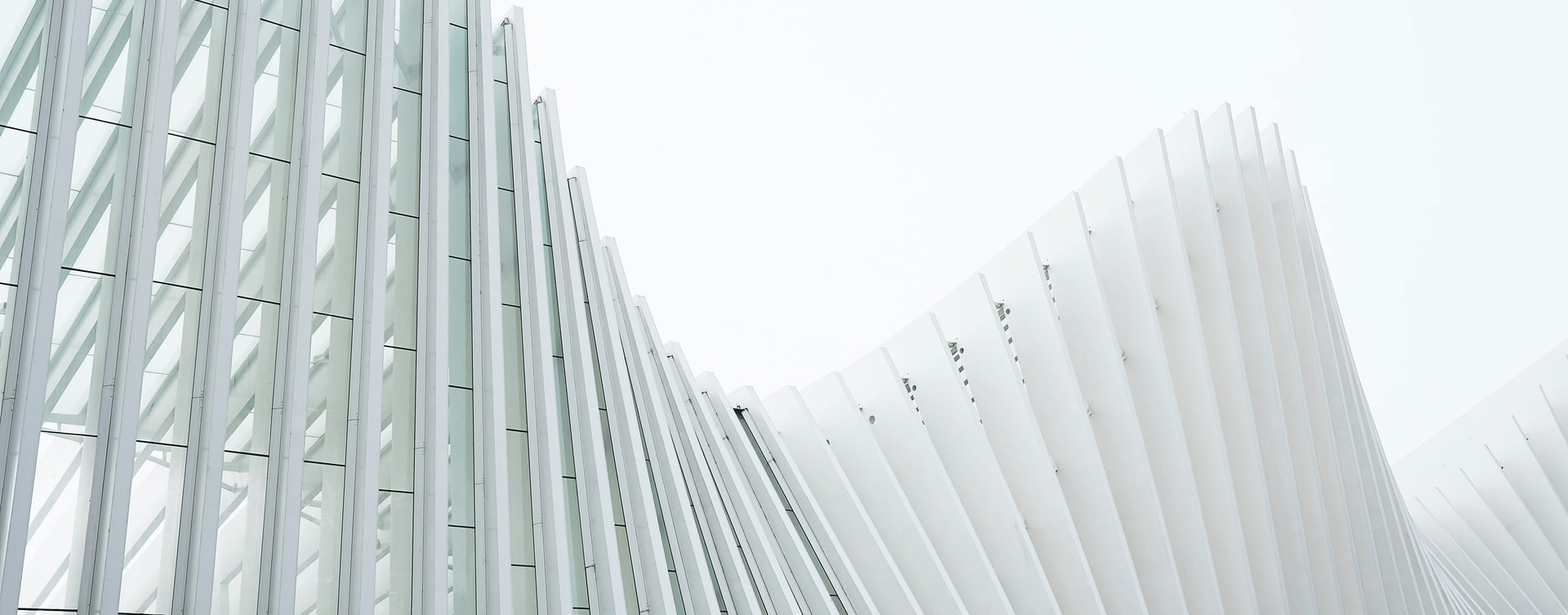
HOOPS Native Platform Powers SIMCON’s Innovative Solution for Demanding Injection Molding Projects
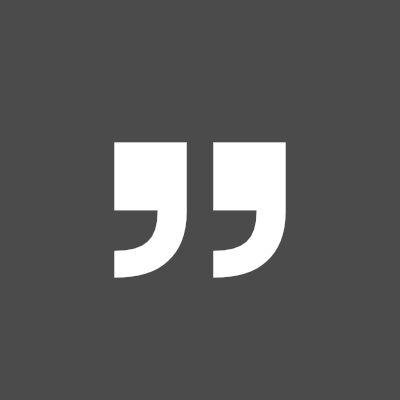
As a company, we always stay very close to our customers and how their needs evolve. Our relationship with Tech Soft 3D has been a win - win so far, and we anticipate they will help us continually find new ways to serve our customers better.”
Dr. Bastiaan Oud, CEO, Simcon
The Challenge
Since its founding in 1988, German company SIMCON has been supporting plastics specialists in improving their parts, molds, and processes. The company’s mission is to help injection molders achieve better results efficiently and sustainably.
“Many of our customers are suppliers who are producing parts for somebody else, like an automotive OEM, an aerospace manufacturer, or a medical equipment company,” said Dr. Bastiaan Oud, Head of Strategy at Simcon. “They’re producing parts that are later assembled into something larger.”
But using injection molding to produce those parts in a way that achieves quality targets–while also balancing other consideration like cost and efficiency–is challenging.
“Injection molding involves shooting liquid-hot plastic into a cavity that is the shape of the part you want to build,” explained Oud. “Once customers get a contract to produce a certain part, they’ll design a physical mold, containing that cavity. Then, they’ll go through a series of tryouts to make sure the part is actually coming out the way it’s supposed to–that it’s filling correctly, and not warping out of shape as it cools down.”
The tryouts often show that corrections are needed. These mold corrections can quickly become very expensive. Oftentimes the mold has to be modified four or five different times to get parts to come out properly, with each correction costing a four digit, or even five digit sum, and taking weeks to complete.
“More often than not, it’s a third-party performing the fixes on the mold–so you have to physically pack up this huge chunk of metal and ship it across the country to them,” said Oud. “They shave down the metal, and then ship it back. It’s not a speedy process.”
Unrivalled 3D Data Input, Output, and Visualization Supports Virtualization
SIMCON felt that customers would benefit from a virtualized process. “With our simulation product CADMOULD and our automation and optimization layer VARIMOS, we help customers virtualize decision-making around part, mold and process design. This way, part and mold designers can test many design variants virtually, before they physically produce the mold,” said Oud. “The fact is, it is much faster and cheaper to change a digital design than it is to modify a physical mold. You can test more variants quickly and efficiently, and produce the best version”.
CADMOULD is a simulation solution that predicts what end results will be obtained, based on part, mold and production process design. For example, it predicts the filling process, as well as part shrinkage and warpage, based on part and mold geometry, the design of the mold cooling system, and the particular material used. VARIMOS is a unique automation and optimization layer, which sits on top of that simulation. It helps users quickly set up many design variants, runs all of them as simulations using CADMOULD, using powerful parallelization. The inbuilt AIthen interprets the results. VARIMOS learns which design and parameter changes have what impact on results, and shows this to the user in a simple way. It also automatically figures out the best configuration to optimize results.
The result is better designs–because users have explored more options and picked a better solution before building the mold. Customers avoid costly mistakes and achieve better quality and manufacturing cost, saving considerable time and money along the way.
To help power its solution, Simcon is relying on the HOOPS Native Platform collection of SDKs. The collection includes three advanced HOOPS technologies for desktop and mobile application development, including HOOPS Exchange for fast and accurate import of over 30 CAD formats, HOOPS Publish for publishing 3D data in a variety of formats, and HOOPS Visualize for powerful3D graphics and visualization.
HOOPS Exchange is key for importing a diverse range of 3D CAD data into Simcon’s simulation engine.
“Our customers are all over the map as far as the type of CAD formats they use, from standard formats like STL, to very niche, application-specific CAD formats,” said Oud. “HOOPS Exchange ensures that our solution can easily bring in those files and accurately convert them into something we can put our own mesh onto, for simulation.”
In addition to assisting with data input, Tech Soft 3D is providing powerful data output capabilities through HOOPS Publish.
“If a customer has simulation results that they want to export as a report to other stakeholders, they can easily generate a 3D PDF that contains the actual 3D model of the object that was simulated,” said Oud. “That’s a very handy way to send simulations to someone who doesn't actually have the software installed, and it makes downstream sharing more accessible.”
Meanwhile, HOOPS Visualize powers an advanced feature within CADMOULD that lets users import an entire mold for simulation and easily visualize it.
“Molds are often very complex, gigabyte-sized CAD files,” said Oud. “We explored several different ways of making it possible for customers to view them, and HOOPS Visualize was a convenient and highly performant way of implementing that functionality. With HOOPS Visualize, the loading times are short, and you can display large models in real time, with incredibly smooth 3D graphics.”
Simcon anticipates rapid growth in its sector in the coming years and has set ambitious global growth targets. In addition to keeping an eye out for talent that can successfully help it scale, the company will continue to look to technological partners like Tech Soft 3D to help it maintain its growth momentum.
“As a company, we always stay very close to our customers and how their needs evolve,” said Oud. “Our relationship with Tech Soft 3D has been a win-win so far, and we anticipate they will help us continually find new ways to serve our customers better.”
Industry: Design and Manufacturing / Plastic Injection Molding / Simulation
Challenge: Injection molders challenged to produce parts for customers in an efficient manner. Significant trial and error required to get parts to come out properly. Molds need to be physically modified multiple times, with each modification taking up to four week and costing four to five digit sum.
Solution: HOOPS Native Platform provides advanced toolkits for CAD data access, 3D data publishing, and 3D visualization, to strengthen capabilities of a powerful simulation and optimization solution for injection molders.
Results: Reduce correction loops required for physical molds by enabling customers to try out more options virtually. Save time and money by simulating performance before committing to a physical design. Make downstream sharing of simulations more accessible, increasing collaboration during the design phase. Smooth workflow: easily import wide variety of CAD formats and provide smooth visualization of even the largest and most complex CAD models. Optimized results sharing: Share interactive 3D results with customers and colleagues, inconvenient PDF form